Home Laser Controls & Instrumentation Division
Supervisory Control and Data Acquisition Systems (SCADAS)
SCADA System for Infrared Free Electron Laser(IRFEL)
Infrared Free Electron Laser (IRFEL) is being developed at MAASD, RRCAT. It consists of various subsystems like vacuum, RF, beam transport line, undulator and other auxiliary subsystems. We have developed supervisory control and data acquisition system for IRFEL. IRFEL control system comprises of 5 Industrial PC (IPC) for various subsystems. Multiple monitors 2/4 are connected to each IPC in order to accommodate GUIs for large number of parameters. For subsystems interface, the IPCs have multiple RS 485 ports, RS 232 ports, Ethernet ports and GPIB ports. The subsystems of IRFEL are as follows:
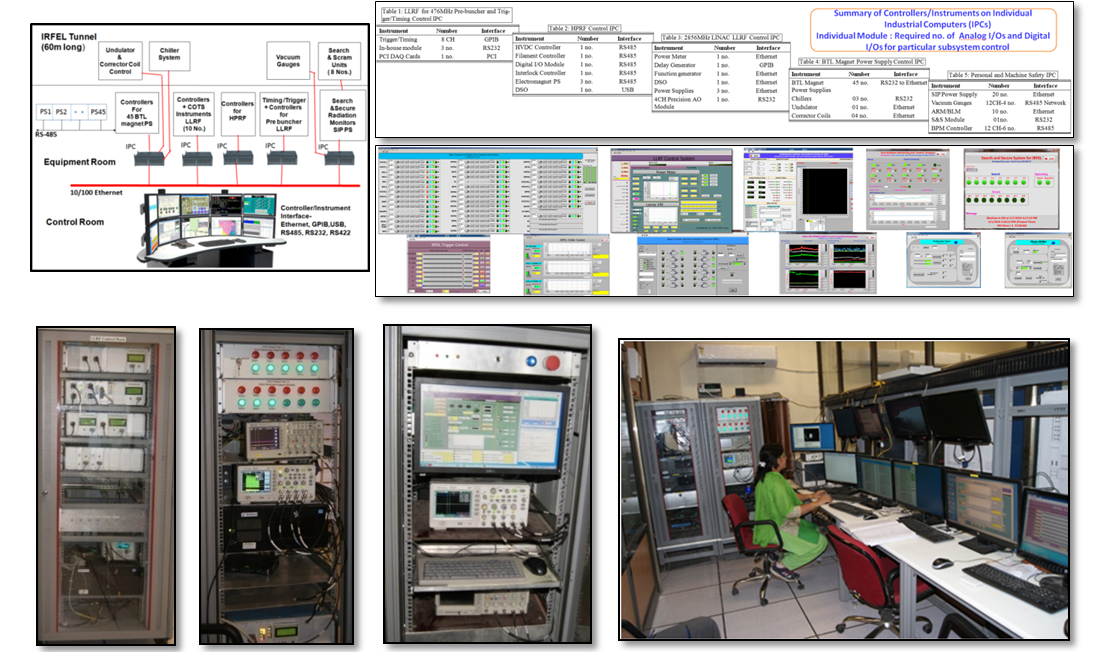
Vacuum System : Vacuum monitoring and data logging system performs vacuum measurement inside various subsystems of IRFEL. Measurement of vacuum is carried out by Bayard-Alpert (BA) gauge. There are four BA gauge monitors, each monitor has four channels. These gauge monitors have RS-485 interface. RS-485 bus network topology is used to connect these four gauge monitors (Agilent XGS 600) to PC in control room. To maintain vacuum in sub-system Sputtering Ion Pumps (SIP) are installed. By monitoring current of SIP power supply one can estimate vacuum in system. Graphical User Interface (GUI) for 20 SIPs Power Supply is developed. The GUI provides Control for operation of SIP over Ethernet network. This GUI measures & display value of SIP current at control room. GUI provides online graph and prepares daily report with date and time stamp.
Software for Radiation Monitoring: To measure radiation in IRFEL tunnel, Tunnel entrance, RF Modulator room & inside the control room various detectors are installed. There are Area Radiation Monitors (ARM’s) and Beam Loss Monitors (BLM’s) installed at various locations. These monitors have Ethernet port for communication with PC. A software module is developed which acquires data from these instruments. This software module is installed on diagnostic IPC located in control room. On IPC online radiation plot is displayed and data is logged with date and time stamp. The software provides alarm in the control room.
Supervisory Control Software & Hardware module for 476 MHz LLRF control: 476 MHz LLRF system requires set points to control RF amplitude, RF phase and other parameters. Apart from this isolated digital I/O signals are required for RF on/off and interlock monitoring. 4 number of in-house developed controllers having 16-no. of isolated analog I/O, 24-no. of digital inputs and 16-no. of potential free contacts (as output) are installed. PCI DAQ card is used for monitoring forward and reflected pulses. Motorized control of pre-buncher tuner is also provided. Supervisory control software module provides graphical user interface to operator so that operator can control operation of LLRF from single point with display of vital operating parameters.
Supervisory Control Software & Hardware for S-Band LLRF and HPRF control: The S-band control involves LLRF control with standard instruments (2 DSOs, 4 Power Supplies, RF generator) and one in-house developed embedded controller. Control for HPRF system consists of setting and monitoring High Voltage DC power supply, chiller units (with RS-232 interface), interlock & status monitoring, filament power supply, thyratron heater power supplies, thyratron reservoir, electromagnet power supplies. For this requirement three in-house developed embedded controllers are installed. Supervisory control software module provides graphical user interface to operator so that operator can control all above operations from single point with display of vital operating parameters.
Beam transport line magnets Power Supplies Control: There are 45 solenoid & quadruple magnets installed on beam transport line from exit of LINAC to entry of Undulator. There are 45 magnet power supply controllers installed in magnet power supply rack. These controllers have RS-485 interface. Supervisory control software module provides graphical user interface to operator so that operator can control operation of these Power Supplies from single point with display of operating parameters. Each power supply has On/Off control, polarity control & fault reset control. It provides fault indication to monitor system as well. These power supplies are working in current control mode. Software provides interface for setting magnet current precisely (with 16-bit resolution) and provides read back of current flowing through magnet (with 16-bit resolution) to user.
Software & Hardware for Beam Profile Monitoring system: Beam Profile Monitor (BPM) consists of phosphor screen, linear translation stage & GigE camera. Phosphor screen is mounted on vacuum compatible linear translation stage which moves the screen in & out of beam path. The camera is mounted exactly opposite of phosphor screen to monitor beam profile. There are 16 BPMs installed at various locations on beam transport line. Linear translation stages have stepper motor for in/out movement of screen. In-house developed multi-channel motor controllers are used to control 16 beam translation stages of BPM’s and 2 motorized slits. These controllers are installed in IRFEL tunnel. We have used RS-485 network (bus topology) to connect these controllers to diagnostic IPC located in control room. There are 16 cameras (for BPMs) installed in tunnel. We have placed Ethernet switch in tunnel to connect these cameras with IPC at control room. On user request software running on IPC sends command to addressed BPM and moves screen in beam path. There are limit switches to detect position of screen of BPM. Once screen position is reached software acquires and displays image of corresponding camera on diagnostic PC. Software provides various measurement image processing tools to enhance beam image and also provides tool for measurement of beam profile. After profile measurement user can send command to move screen out of beam path. There is provision to store beam profile image, measured profile parameter with date & time stamp.
Software for Trigger/Timing System of IRFEL: Trigger and timing circuit of IRFEL uses Berkley Nucleonics Corporation(BNC 575) make 8-CH Programmable delay/pulse generator. This generator has GPIB interface. This generator is integrated with RF control station. Delay generator receives master trigger from LLRF system and generates six delayed trigger signals for synchronization between various systems of IRFEL. Software module developed provides graphical user interface for operator to set value of delay between various channels.
Search and Secure System: A hardwired Search & Secure (S&S) system is installed consisting of search and secure units at 8 locations. It also has two door interlocks in place. This S&S system is connected with micro-controller based S&S monitoring system. This monitoring system reads status of various S&S, door interlock units. This monitoring unit has RS-232 interface. Supervisory software running on diagnostic IPC communicates with monitoring unit and provides online status of search operation for operator sitting at console. During search operation software automatically plays (using sound card of PC) pre-recorded audio messages/warnings. This audio output is amplified and broadcast in tunnel, modulator room and control room of IRFEL. Automated announcement system eliminates human errors.
Electron gun, LINAC, Undulator & its corrector coils are three major sub-systems of IRFEL. These three sub-systems have connectivity over LAN port. LCID provided dedicated supervisory control software with graphical user interface (GUI) for operation of these systems. It also provides read back of parameters for operator.
Miscellaneous systems: There are various sub-systems which are essential for operation.
Precision chillers: There are four precision chillers with RS-232 interface, which are placed inside the tunnel. We have connected these chillers with Ethernet to RS-232 converter (eight port). Control software is developed to set LCW temperature and to measure temperature of LCW inside coolant circuit. The software plots LCW temperature against time for operator.
Nitrogen pressure monitoring system in RF wave guide: A micro-controller based 8-channel, 12-bit, data acquisition system is designed and installed in tunnel to monitor pressure & temperature of Nitrogen gas in waveguide.
Control software & hardware for RF Phase Shifter unit: Two RF phase shifter units are installed in LINAC of IRFEL. The RF phase shifter has motor to vary phase between input & output port. This phase shifter also has feedback signal corresponding to phase variation. In-house developed phase shift controller with motor driver, 12-bit analog input to measure phase shift is developed and installed near the phase shifter unit. This unit has RS-485 interface. Software module developed provides graphical user interface for operator to adjust phase shift and provides read-back of phase shift.
SCADA System for CUTE-FEL (Compact Ultrafast Terahertz Free Electron Laser)
A supervisory control system is developed for CUTE-FEL project at RRCAT. The setup consists of Pulsed thermionic gun, Linear Accelerator (LINAC), Beam transport line (BTL) and undulator assembly. There are various ancillary systems, which takes care of vacuum in LINAC and BTL, gas pressure in wave-guide assembly, radiation monitors etc.
We have designed a SCADA system based on Master-Slave architecture. The distributed architecture has a Master PC with 8 subsystem slave controllers (MCS-51 based), 4 vacuum gauges, RF signal generator, BPM controller connected to it in star topology over a RS485 network. The Master PC provides a Man Machine Interface (MMI) for machine operation from a remote control room. There is a separate Supervisor PC to monitor critical beam parameters. The Master PC connects to Supervisor PC on a 100 Mbps Ethernet link. The Supervisor PC has 2 DSOs to monitor the forward & reverse pulses and RF Power meter connected over a GPIB network. The Master PC houses dual monitors for displaying large no. of parameters. We have incorporated various safety features in software as well as hardware for safe operation of the system.
Control system for Vertical Test Stand
RRCAT has developed Vertical Test stand to evaluate performance of indigenous developed Super Conducting Radio Frequency Cavities (SCRFC). As part of this activity a PLC based control system is developed (in association with ACD) to monitor & control various parameters of the process. The control system is based on Siemens make S7-300 PLC with 16-channel Digital I/O, 8-channel Analog I/O. Various monitoring devices for temperature, level with digital interface are also interfaced with PC. This control system has PC with Graphical User Interface to control and monitor VTS cryogenics parameters. A graphical User Interface has developed by using WinCC software.
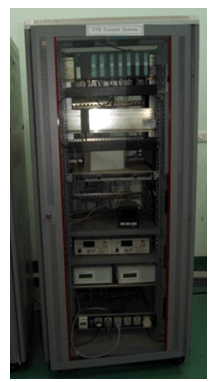
Data Acquisition and Control System for MOVPE Growth
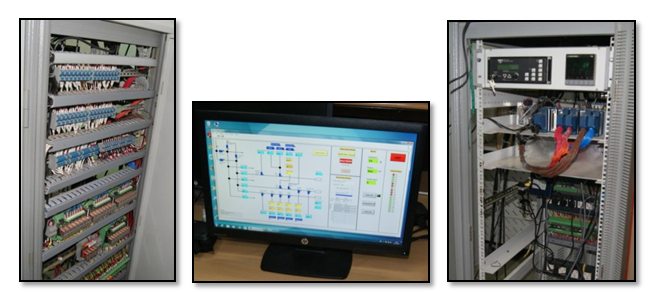
MOVPE machine consists of reaction chamber where various gases are mixed in controlled manner to achieve wafer growth. Pressure and temperature of reactor chamber is controlled precisely to maintain the quality of growth. The mixing of gases is carried out with the help of solenoid valves and mass flow controllers (MFCs). There are 32 MFCs, 24 solenoid valves, vacuum system, temperature controller and pressure controller unit. A PAC based system is developed which provides set point and gets read back from all the field devices. Labview based SCADA software runs on PC which provides GUI to operator to write recipe for wafer growth. Each step of recipe includes setting of state of all valves, MFCs, temperature/pressure and interlock conditions required for the particular stage of growth. 100s of such steps can be entered in a recipe, as per requirement. The software automatically takes care of growing the crystal as per the fed recipe. The recipes can be fed offline and then used as per availability of machine. The growth process takes from minutes to hours for completion and is completely automated.
PLC based control unit for Copper Vapour Laser System
Programmable Logic Controller (PLC) based control unit is developed for monitoring and control of the operation of copper vapour laser system. In PLC program different interlocks have been incorporated to operate the laser system safely and reliably. Human machine interface with TFT display and touch input is provided to acquire user inputs and display status of different parameters.
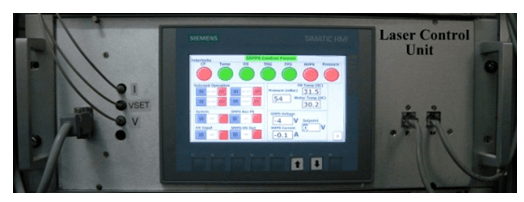
Automation of Precise Synchronization Control for Laser Chain
Laser units in MOPA configuration needs to be synchronised precisely for optimized performance. Labview based setup is developed that provides close loop control for precision synchronization of Copper laser MOPA system. The software provides delay setting with sub-nanosecond precision and user friendly graphical user interface (GUI). It also has provision for setting copper laser parameters like pulse repetition rate, and monitoring laser power stability over long operating periods.
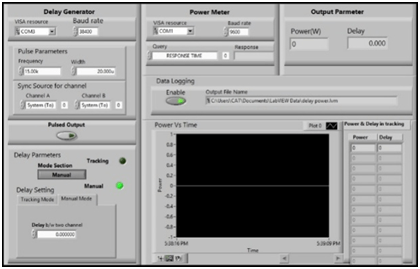
Dye temperature control unit for tuneable dye laser
Thermoelectric cooler based dye temperature control unit has been developed which provide dye solution temperature stability better than ±0.2 OC for the temperature at user selectable temperature up to 5 OC below from ambient. This unit is interfaced to the PC using RS232 interface and software is developed by which user can set the desired temperature and monitor the current temperature with temperature logging facility.
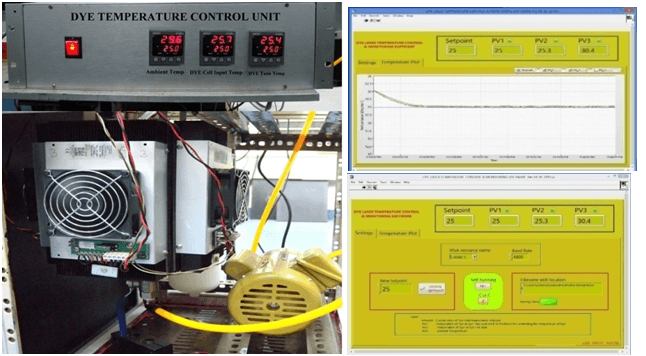
|