|
Laser Materials Processing Division |
Failure Analysis of In-house Components
Failure Analysis of Stainless Steel Sheets of Heat Shield Assembly of a Vacuum Degassing Furnace
History of the component:
- RRCAT has a ten-year old vacuum degassing furnace with maximum operating temperature of 800 °C. The heat shield assemblies comprised of one molybdenum sheet in the front (facing the hot zone), followed by four numbers of stainless steel (SS) sheets, fastened with nut, bolts and ceramic spacers. The thickness of each sheet was 1 mm.
- As a part of preventive maintenance of the furnace, the end shield assemblies were removed from the furnace and disassembled. 304 SS sheets (75 cm x 75cm x thickness), which formed part of heat shield, were covered with strongly adhered black oxidized scale in central region.
- For removng black scales, SS sheets were subjected to chemical cleaning involving:
- cleaning in trichloro ethylene (TCE) for several hours which failed to dissolve black scale,
- exposed to 20%HNO3+1.5%HF solution for about total 8 hours with intermediate removal and scrubbing in the interval of 1-2 hours.
Cause of degradation:
- Damage was caused by severe sensitization of edge region.
- The sensitized part of SS sheets underwent extensive intergranular corrosion (IGC) (Fig.2) during chemical cleaning in 20% HNO3+1.5% HF solution.
Suggested remedial measures suggested to avoid similar failures in future:
- use of type 316L or stabilized grades of austenitic SS sheets,
- use of two Mo front sheets in place of one and
- use of mechanical cleaning in place of chemical cleaning.
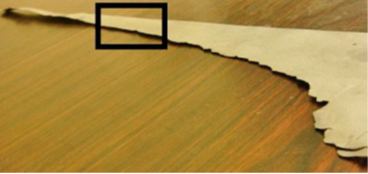
|
Fig.1: Stainless steel strip separated from one of the chemically cleaned stainless steel sheets used for failure analysis. The rectangular mregion shows the location of specimen extracted for metallography. |
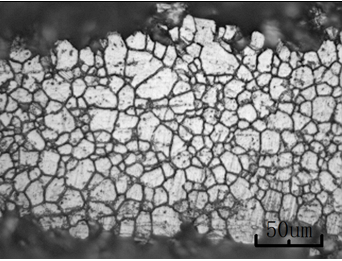
|
Fig.2: Sensitized part of SS sheets underwent intergranular corrosion (IGC) |
Publication:R. K. Gupta et al., Practical Metallography, 58, 2021, 49-61.
|
|
|