Diffusion bonding of tube to tube joint (Titanium - SS 316)
Tube-Tube lap joint of Titanium & SS316 obtained by diffusion bonding. This method of assembly of all components (shrink fit assembly of machined tubes of Ti and SS 316, SS plug and other fixtures) exploits different CTE of various materials to generate the compressive stress between the faying surfaces of Ti and SS at the joining temperature without application of any external loading. The assembly of all components is exposed to 900°C for 120 min in a vacuum furnace.
Highlights:
06 numbers of diffusion bonded joints of Titanium tube to SS tube were prepared with different wall thickness of Ti- tubes (1.2 mm, 1.5 mm, 1.8mm two Nos each). Figure below depicts the Ti – SS diffusion bonded joints
All the specimens exhibited vacuum leak rate better than 10E-10 mbar.lit/sec. Shear strength of the joints based on nominal joint area was in the range of 40-50 MPa. Optical microscopic examination and SEM-EDS analysis of the joint cross-section show sound joint formation at the interface with a inter diffusion zone of 3-5 microns.
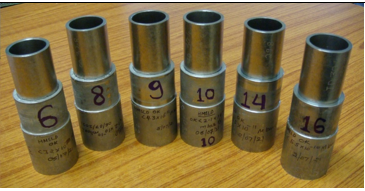 |
Tube -tube Ti-SS diffusion bonded joints. Top: Ti tube; Bottom:SS 316L tube |
|
|
SEM image of the joint cross section (Left) and the associated EDS elemental mapping (right) of diffusion bonded joint (rectangular marked interface zone) of Ti tube to SS316 tube. |
SEM image of the joint cross section (Left) and the associated EDS elemental mapping (right) of diffusion bonded joint (rectangular marked interface zone) of Ti tube to SS316 tube. |
Vacuum brazing of titanium/316L stainless steel transition joint for application in helium vessel of superconducting RF cavities
Superconducting radiofrequency (SRF) cavities would form important part of the proposed Indian Spallation Neutron Source and Accelerator Driven System. The high beta 650 MHz SRF cavity made of niiobium would be enclosed in a cylindrical vessel made of Titanium to hold liquid helium (LHe). The LHe inlet supply line and return helium gas pipe line of the helium vessel would be made of 316L stainless steel (SS). This requires a bi-metallic tubular transition joint between Ti and 316L SS, operating at LHe temperature. Vacuum brazing and explosive welding are potential processes for joining these two dissimilar metals (Ti-SS), as fusion welding leads to extensive cracking. In the case of brazing, the large mismatch in mean coefficients of thermal expansion (CTE) between Ti (8 x 10-6 µm/m.K) and 316LSS (16 x 10-6 µm/m.K), requires control of braze joint thickness at the brazing temperature through proper design and fabrication of fixtures for the given geometries of the components to be brazed.
Highlights:
Vacuum brazing of titanium pipe to nickel-plated 316LSS flange with BVAg8 filler resulted in sound transition joint with satisfactory shear strength of about 50-60 MPa and uniform joint thickness of about 50 +/- 10 µm. Notable features of the brazing process include use of
- 5-10 µm thick nickel plating as a diffusion barrier on SS part for preventing possible iron migration towards titanium while improving surface wettability for BFM and
- Use of 304 SS plug, shrunk fit into Ti pipe, for achieving dimensional and profile accuracy of Ti pipe during machining while also controlling joint gap during brazing process.
- The brazed assembly displayed acceptable level of hermeticity (better than 2 x 10-10 mbar.lit/sec) and also successfully sustained six thermal cycles between room temperature and liquid nitrogen temperature (77 K).
|