Home Page Superconducting Cavities Development Division
Development of SCRF Cavity Infrastructure Facilities
RRCAT has taken up a program on R&D activities of 1 GeV, high intensity superconducting proton linac for Indian Facility for Spallation Research (IFSR). The most significant limitation of normal conducting RF cavities is the thermal load for high duty cycle operation. Above a certain limit of such thermal load it is not possible to remove the heat from the cavity walls without losing performance or reliability. Development of SCRF cavities is an important accelerator technology to provide efficient, high current and high gradient accelerating structure for nearly all major high duty proton/ H- accelerator projects around the world. Infrastructure facilities have been established in the areas of SCRF cavity fabrication, testing and dressing. A dedicated building has been constructed to house the SCRF cavity infrastructure facilities. Major facilities setup at RRCAT includes:
SRF cavity fabrication facility
1.Electron Beam Welding Machine
The SCRF cavities are made using blanks cut from Niobium (Nb) sheets. A detailed quality control is needed for checking the quality of Nb sheets received from the manufacturer for pits, scratches or inclusions of foreign material prior to use in forming cavities. The cavity parts are joined together using Electron Beam Welding (EBW) Machine in high vacuum to minimize contamination during welding. A 15 kW Electron Beam welding machine has been installed and commissioned at SCDD for the purpose.
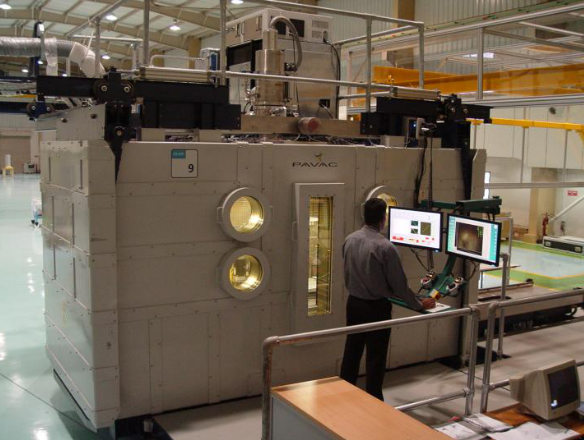
15kW Electron Beam Welding Machine
SRF cavity testing facility
1.Cavity temperature mapping fast thermometry system
The functional performance of superconducting cavities becomes limited by various mechanisms (eg; thermal breakdown, multipacting, field emission, etc.). These systems pose major problems in the operation of high potential (Eacc) cavities. To understand these mechanisms limiting the functional performance of the superconducting cavity, a silicon diode based thermometry system has been developed. These thermometer is mounted on the equator region of the outer wall of superconducting radio frequency cavities. During cold testing (at 2K), when a cavity is charged with radio-frequency electrical power, errors during the manufacturing of the cavity lead to the formation of thermal fields, which are detected by this thermometry system. After determining the type of error, the inner surface of the detected area is corrected after microscope examination at room temperature.The thermometry system is operational and is used regularly during VTS testing of SCRF cavities at 2K.
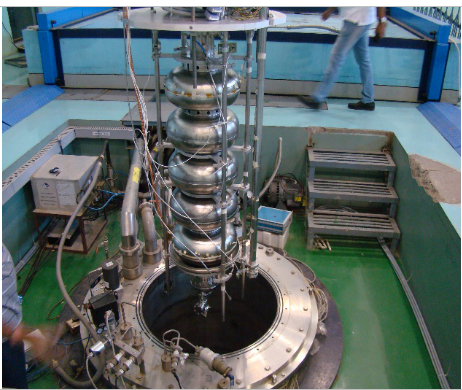
650 MHz five cell cavity equipped with temperature mapping system at RRCAT VTS Facility
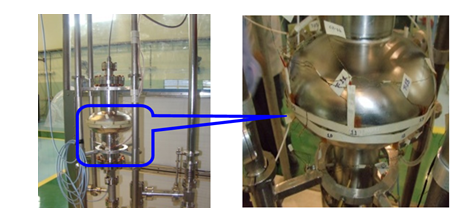
VTS testing of 1.3 GHz, β=1 single cell Nb cavity at 2 K
Material characterization facility
1.Measurement of “Residual Resistivity Ratio” (RRR) of Niobium
An indigenous facility has been developed to measure the “Residual Resistivity Ratio” (RRR) of Niobium. This test is very useful for gross qualification of niobium for bulk resistivity from various sources and also to monitor the variation in RRR during any of the cavity processing stages (such as welding, forming, chemical treatment, centrifugal barrel polishing etc.). This facility is routinely operational and has been calibrated with bench mark samples from FNAL and CERN.
SRF Cavity Dressing Infrastructure
Cavity dressing requires an important infrastructure known as environment-controlled welding glove box. The glove box environment produces the best quality TIG welds that meet ASME Boiler and Pressure Vessel Code. The glove has 12 glove-ports for welding from various locations of dressed cavity with 6 viewing window. This welding glove box has been installed, tested and commissioned recently at RRCAT with achieved Oxygen level <10 PPM and relative humidity (RH) level <2%, which are better than the required level of 20 PPM for Oxygen and 15% of RH. This is an important milestone towards the development of dressed SCRF cavity.
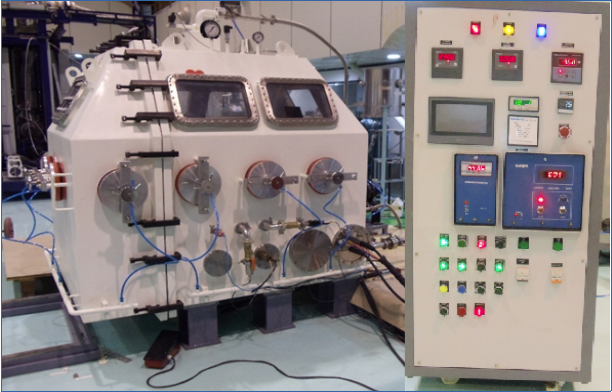
Controlled environment Welding glove box
Further a specially designed insertion bench also known as medium bertha is developed which is crucial for proper alignment of various dressing components and cavity before loading it into the glove box.
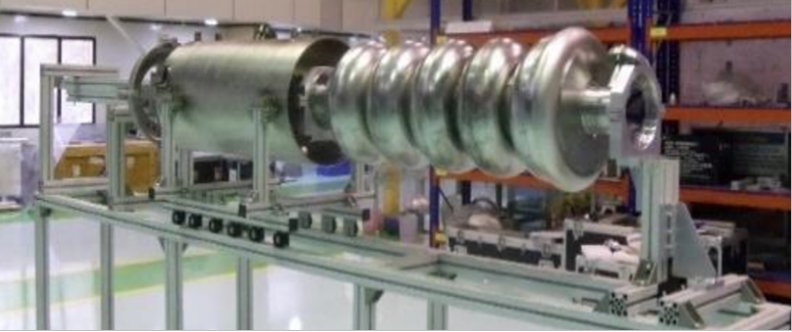
Alignment and assembly fixture- ‘ medium bertha’
Dressing of SCRF cavity:
After initial qualification of ‘bare’ five-cell SCRF cavity in VTS (Vertical Test Stand), the cavity is required to be jacketed or dressed with helium vessel, end caps and bellow. Recently, an important milestone was achieved by RRCAT, when successfull ‘jacketing’ of first HB650-501 five-cell SCRF cavity was completed.
Crucial technical requirements for SCRF cavity dressing include preventing the degradation of multi-cell SCRF cavity field flatness and keeping the drift in cavity frequency within range of slow tuner for this a “frequency monitoring and alarm” system was designed and developed.
| |
Cavity dressing in progress | Completion of Cavity dressing |
Successful dressing of HB650 Five-cell SCRF cavity has been done for the first time in the country and very first in the world for this beta 650 MHz β = 0.92 five cell cavity. This is an important milestone towards dressing of five-cell cavity for its further integration in to HTS for high power testing.
|